Preventive maintenance (PM) helps avoid maintenance problems by detecting potential problems early and solving them before they become expensive repairs. Preventive maintenance is a systematic monitoring, testing and repair of defective components in equipment. Maintenance aims to prolong its life by eliminating possible failures. How does preventive maintenance work? What are their types and benefits?, That's what we'll recognize in this article, read on.
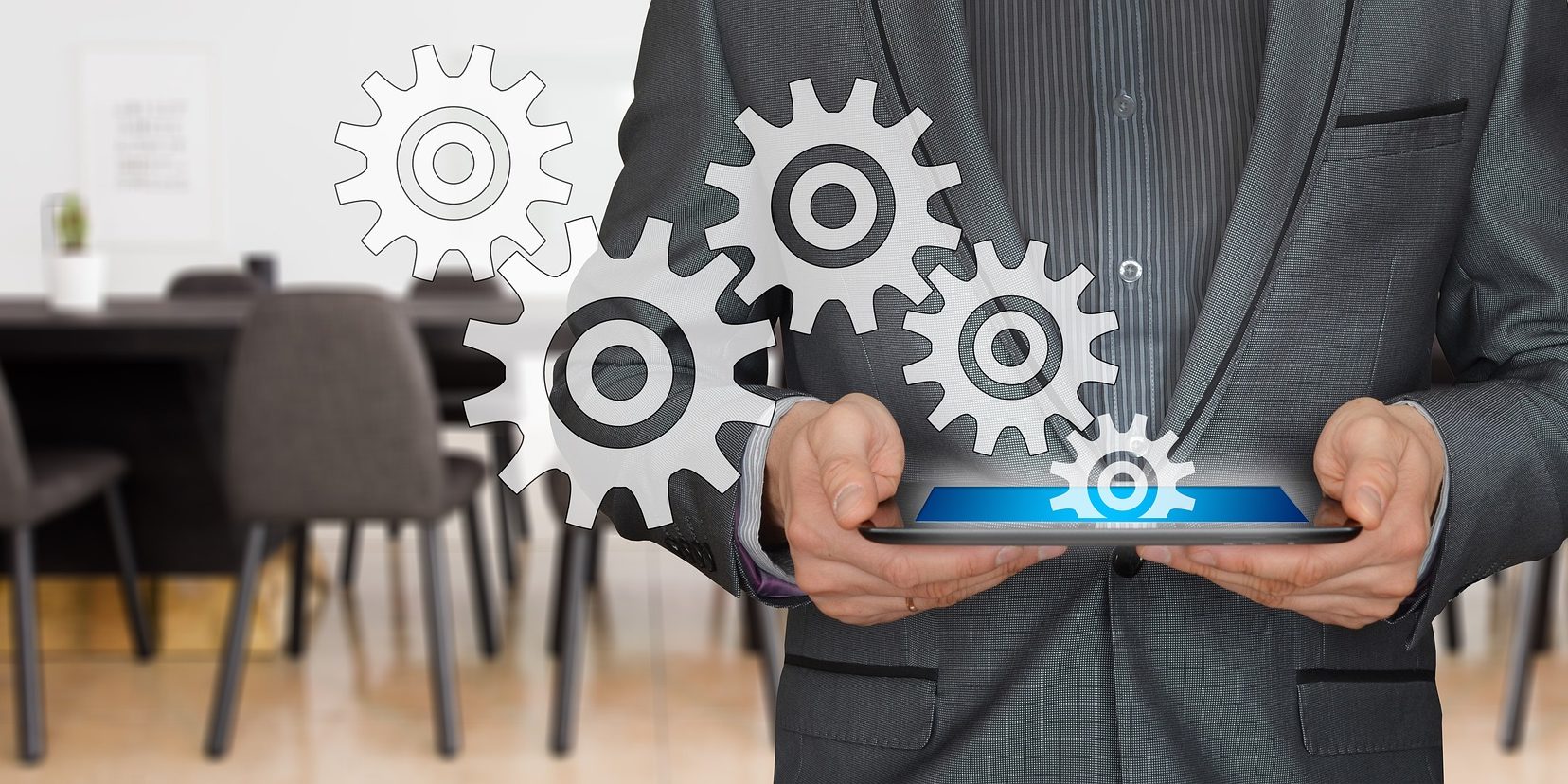
How does preventive maintenance work?
Through machine learning, operational data analyses and predictive asset health control, engineers can improve maintenance and reduce reliability risks to factory or business operations. Programs designed to support preventive maintenance help produce stable operations, ensure compliance with safeguards and solve problems affecting production - before they occur.
A successful maintenance strategy requires planning and scheduling equipment maintenance before a problem occurs, a good preventive maintenance plan also includes keeping records of past inspections and equipment servicing.
Due to the complexity of maintaining the preventive maintenance schedule for a large amount of equipment, many companies use preventive maintenance programs to organize the required preventive maintenance tasks.
What are the types of preventive maintenance?
There are 3 main types of preventive maintenance, each built around the concept of planned maintenance, although it is organized and scheduled differently, to suit the purposes of different business operations, the details of which are as follows:
1. Mandatory/non-mandatory tasks
Mandatory tasks are those that must be performed as soon as they are due and will often include critical safety checks, and non-mandatory tasks are still important, but can be delayed without resulting in severe failure or decreased performance, the preventive maintenance checklist should divide tasks into mandatory or non-mandatory.
2. Hierarchical/non-hierarchical tasks
Hierarchical tasks occur when maintenance is set for a maturity date but is not completed and overlaps with later scheduled maintenance in this case, if the new preventive maintenance mission is due the previous task is cancelled, the cancellation must include a note to explain this and the new task must include the original due date to monitor the mission's delay Some companies prefer a non-hierarchical structure, eliminating the need to observe the original mission lost and taking the new date as a baseline.
3. Inspection and targeted tasks
Survey tasks require examinations before converting results into work orders for planned maintenance to fix any problems detected. Task-oriented task management allows for minor repairs and adjustments at the time of examination, reducing the amount of work to be written as work orders in the survey paper.
When is preventive maintenance required?
Precise requirements for preventive maintenance will vary depending on the equipment and process you perform, industry uses standards to help determine maintenance schedules so that assets do not work with failure, this guidance will also cover the type of inspection or maintenance required.
Ideally, following guidelines set by manufacturers or standards, the preventive maintenance schedule should ensure proactive maintenance rather than having to resort to interactive maintenance when something has already begun to fail.
Following this type of predictive maintenance schedule, through tasks such as case monitoring, requires accurate recording of inspections and service versus understanding the life span of a particular piece of equipment, these records will help determine when preventive maintenance is required.
Examples of preventive maintenance
Industrial situations rely heavily on regularly scheduled maintenance to remain fully productive and free of costly and time-consuming mechanical breakdowns.
The term "preventive maintenance" covers a wide range of prohibited public activities and tasks, each component of production within the system will require a certain level of regular service, and this equipment will usually need to be cleaned and lubricated at least, in other cases, a more comprehensive service may be required - including heavy refurbishment, repair or even replacement of certain parts.
At a higher level, preventive maintenance also involves the provision of maintenance for the physical plant that includes various production systems, the general tasks associated with this type of preventive maintenance include ensuring that the heating, ventilation and air conditioning system is in good working condition, that all electrical systems are functioning and compatible with code standards, and all necessary lighting is functioning properly.
Benefits of preventive maintenance
While following the preventive maintenance strategy, you will receive many advantages including:
Reduce the risk of breakdowns
Reducing crash risk is another key feature of preventive maintenance, in fact, most of the benefits mentioned here occur primarily as a result of reduced crash risk, waiting for maintenance to be performed until failure puts your facility at risk of loss of productivity and damaged reputation.
Only about 10% or less of industrial equipment is truly wear and tear from proper use - this means that 90% of mechanical failures are caused by preventable problems, and can be avoided with a good preventive maintenance plan, by scheduling maintenance proactively, you can significantly reduce the risk of equipment failure, giving you peace of mind as a leader of installations.
Prolonged asset life
Arguably, the most important benefit of preventive maintenance is to prolong the asset's shelf life, keeping your equipment in good condition allows it to operate longer, reducing costs. MTBF - average time between failures - is a common key performance indicator used by facility leaders to make informed maintenance decisions, lets you track information like MTBF planning preventive maintenance at the right moment, capturing equipment before a failure.
The power of a good downtime tracking system is so influential that 78% of companies that track and implement preventive maintenance reports experience an increase in the life of their devices.
Increased efficiency
Along with longer lasting equipment, equipment undergoing routine preventive maintenance works more efficiently, the effectiveness of OEE universal equipment is a commonly used key performance indicator for maintenance management which measures efficiency, OEE classifies equipment into three categories: availability, performance and quality.
Reduce unplanned downtime
Whether you decide to rely on interactive or preventive maintenance, machine breakdown is inevitable when maintenance is carried out, however, downtime can be greatly reduced by scheduling maintenance in advance using a tight plan, in case of reactive maintenance repair, machine failure time may be extended by waiting times to know specialist mechanics or the time to charge the necessary parts.
When you perform the required maintenance, you have the opportunity to schedule the procedure in time for you and your facility (for example, when passengers are out of the building or operations are over for the day), reducing disruptions in production and efficiency.
Preventive maintenance programmes
The preventive maintenance program, such as the Maintenance Operations Management System (CMMS) of fekrait Software, is a key tool to move away from interactive maintenance and daily disruptions. By working on our program, maintenance teams will be able to reduce costs and increase running time.
The program ensures that scheduled maintenance of assets, installations and equipment can be performed automatically and customized to the preferred contractor through a smooth and automated method on an ongoing basis For example, repetition may vary such as an asset requiring a monthly maintenance check versus another that may be quarterly, In this case the job assignment is automatically assigned to the preferred contractor to operate when the frequency appears This will usually form part of your work order program and start with a job application form.
The system also reduces data entry by eliminating the need to create new tasks for each PM table, as preventive maintenance software simply connects PM mission to multiple PM schedules.
Conclusion:
Preventive maintenance is the process of performing regularly scheduled maintenance activities to help prevent unexpected breakdowns in the future. Simply put, it is about repairing things before they break, and a successful maintenance strategy requires planning and scheduling of equipment maintenance before a problem occurs.
Topics that may concern you:
reference
1. <<5 Types Of Preventative Maintenance In Commercial Facilities>>، iotacommunications
2. << What are the types of preventive maintenance?>>, YouTube
Comments
13 Jun 2023 12:53 AM
محمد
يارك الله جهودكم
13 Jun 2023 12:55 AM
محمد امين
شكراللمعلومات
13 Jun 2023 12:59 AM
ISLAM
موفقين
Add New Comment